Why Machine Tool Fixtures Are Essential in Modern Manufacturing?
- mitsubishielectric1
- Jul 9
- 4 min read
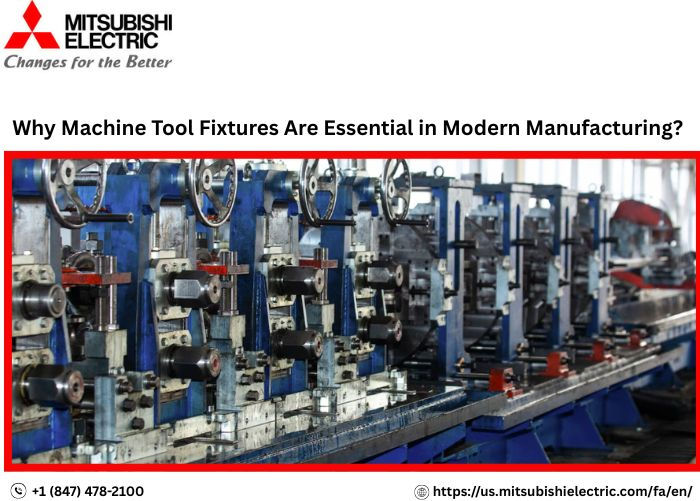
In the high-speed production world of today, accuracy and efficiency are not just desirable - they're critical. If you're working with aerospace components or assembling car parts, every second and every millimeter counts. That’s why machine tool fixtures play such a vital role on the factory floor. These seemingly simple tools are the backbone of precise machining and one of the key enablers of automation, especially when used with automated line robots.
Let's talk about why machine tool fixtures are a requirement on the contemporary production floor today, and how they shape the future of smart production lines.
What Are Machine Tool Fixtures?
A machine tool stability is a special tool that is used to catch, support, and position a workpiece in a functioning operation. Unlike a common-purpose clamp or vice, stability is custom-decoration, which is to firmly hold the parts in the exact position required for cutting, drilling, or milling - without shifting pressure. It provides stability and accuracy in every operation. In short, stability acts as a link between raw materials and an innocent finished product.
The Role of Machine Tool Fixtures in Precision Engineering
Modern manufacturing demands tolerances in microns. One slight misalignment will render the entire lot of parts useless, leading to costly waste and production delays. Machine tool fixtures avoid loss by allowing precise positioning, which allows machine tools to operate at maximum accuracy.
In critical uses like the production of medical devices or aerospace, where tolerances are not allowed, the use of good-quality fixtures is discretionary. The fixtures allow for the workpiece to be completely stationary even with advanced, multi-axis machining operations.
Enabling High-Volume Production
Speed is another area where machine tool fixtures shine. In a high-volume production plant, the ability to load and unload workpieces very fast and accurately is critical. Fixtures allow that process to be automated, reducing manual touch and cycle time.
A well-conceived fixture streamlines workflow and decreases downtime. It allows the same machine operation to be achieved on hundreds or thousands of parts without resetting or realigning each time - saving both time and labor.
Seamless Integration with Automated Line Robots
As factory smart, industry develops in a 4.0-capable environment, coordination between machine tool fixtures and automated line robots is becoming increasingly important. Automatic robots can apply efficient repeating operations with high accuracy and speed. However, their effectiveness largely depends on how well a workpiece is presented and clamped during the process.
This is the place where the fixtures become mission-critical. Robot loading and unloading fixtures can significantly affect the efficiency of an automatic cell. In a CNC machining line, for example, an automatic robot can be an arm that will pick up the raw material, load it into a stable, and start the machining cycle - all automatic.
Custom fixtures with quick-change features are usually used to reduce the setup time in robotics and get maximum uptime. Additionally, sensors and smart feedback systems within the fixtures can provide real-time data to the robot's adaptive machining methods and future maintenance.
Reducing Human Error and Increasing Safety
In traditional machining setups, part status and clamping are the responsibility of human workers. It opens the door to variability and human error. Not only does stability remove this variability, but it also improves workplace security.
In automated systems, fixtures reduce the risk of employees moving machine parts, sharp-cutting equipment, or dangerous materials. Combined with automated line robots, fixtures improve the work environment to become safer and more ergonomic.
Flexibility and Modularity in Advanced Fixture Design
Those days are gone when machine tool fixtures were static and dedicated to one task alone. Today, flexibility is what advanced manufacturing requires. Companies are acquiring reconfigurable and modular fixture systems that can be rearranged with ease to accommodate new products or prototyped ones.
Such flexibility is particularly useful in large-scale production features such as auto plants, where model changes often occur and run from small to small. Modular fixtures can be reused in various jobs; costs can be reduced, and infection between production lines can be simplified.
Supporting Quality Control and Data Collection
High-end fixtures can also provide in-process inspection and quality monitoring. Integrated probes and sensors can monitor parameters such as clamping force, positioning, and thermal expansion. This data can be fed back to the system to run real-time adjustments to increase the quality of the part and reduce scrap.
In an industry 4.0 world, machine tool fixtures are no longer inactive holders, but integrated, active participants in the data-operated manufacturing process.
Conclusion
While machine tool fixtures cannot attract a spotlight such as robotics or AI-operated analytics, their impact on modern manufacturing is deep. From ensuring pinpoint accuracy to enabling high-speed automation with automated line robots, some fixtures are the unsung heroes that keep production lines running smoothly.
In an era where speed, accuracy, and sharpness are top competitive benefits, investing in first-class machine tool fixtures is not just smart - it’s essential. As manufacturers continue to embrace smart technologies and digital transformation, they expect machine tool fixtures to evolve right alongside them, playing a pivotal role in shaping the factories of the future.
Comments