Streamlining Operations with Automated Conveyor Systems
- mitsubishielectric1
- Apr 17, 2024
- 4 min read
In today's fast-paced manufacturing landscape, efficiency and productivity are paramount to staying competitive. As factories and warehouses strive to meet increasing demands while reducing costs, automation has become a key strategy for streamlining operations and improving overall efficiency. One of the cornerstone technologies driving automation in material handling is automated conveyor systems. These systems, integrated with advanced technologies like Mitsubishi factory automation and factory robots, play a crucial role in optimizing material flow, increasing throughput, and enhancing overall productivity. Let's explore how automated conveyor systems are revolutionizing material handling automation and transforming the modern industrial landscape.
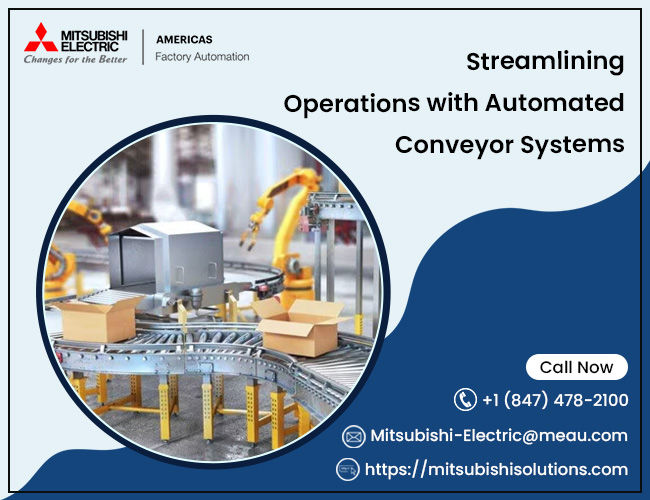
The Evolution of Material Handling Automation
Material handling automation has undergone a significant evolution in recent years, driven by advancements in technology and the need for greater efficiency and flexibility in manufacturing and logistics operations. Traditional material handling methods, such as manual labor and static conveyor systems, are increasingly being replaced by automated solutions that offer greater speed, accuracy, and reliability.
Automated conveyor systems lie at the heart of modern material handling automation, serving as the backbone for transporting goods, components, and products throughout the production process. These systems utilize a combination of conveyor belts, rollers, motors, sensors, and control systems to automate the movement of materials along predetermined paths, eliminating the need for manual intervention and streamlining the flow of goods from one point to another.
Key Components of Automated Conveyor Systems
Automated conveyor systems consist of several key components that work together seamlessly to facilitate material flow and optimize operational efficiency:
Conveyor Belts: Conveyor belts are the primary means of transporting materials within automated conveyor systems. They come in various configurations, including flat belts, modular belts, and roller belts, to accommodate different types of materials and applications.
Rollers and Rollers: Rollers and rollers provide support and guidance for conveyor belts, ensuring smooth and reliable movement of materials. They can be powered or non-powered, depending on the specific requirements of the application.
Motors and Drives: Motors and drives power the movement of conveyor belts and control their speed and direction. Advanced motor technologies, such as variable frequency drives (VFDs) and servo motors, enable precise control and energy-efficient operation.
Sensors and Control Systems: Sensors and control systems monitor and manage various aspects of automated conveyor systems, including material flow, speed, position, and safety. They can detect obstructions, jams, or anomalies and trigger appropriate responses to ensure smooth operation and prevent downtime.
Advantages of Automated Conveyor Systems
Automated conveyor systems offer a wide range of benefits for manufacturers and logistics providers looking to streamline material handling operations:
Increased Efficiency: By automating the movement of materials, automated conveyor systems reduce reliance on manual labor and minimize the risk of human error. This leads to faster throughput, shorter lead times, and increased overall efficiency.
Improved Accuracy: Automated conveyor systems provide precise control over material flow, ensuring that products are delivered to the right place at the right time with minimal deviation. This improves accuracy and reduces the likelihood of errors or inconsistencies in production.
Enhanced Flexibility: Unlike traditional conveyor systems, which are often fixed in place, automated conveyor systems can be easily reconfigured or adapted to accommodate changes in production requirements or layout. This flexibility allows manufacturers to respond quickly to evolving market demands and optimize their operations accordingly.
Optimized Space Utilization: Automated conveyor systems are designed to maximize the use of available space, allowing manufacturers to make the most efficient use of their facilities. By reducing the need for aisles and storage space, automated conveyor systems help optimize floor space and increase storage capacity.
Improved Safety: Automated conveyor systems incorporate advanced safety features, such as emergency stop buttons, safety interlocks, and protective guarding, to ensure the safety of workers and prevent accidents or injuries. This helps create a safer working environment and reduces the risk of workplace incidents.
Integration with Mitsubishi Factory Automation and Factory Robots
Automated conveyor systems are often integrated with other advanced technologies, such as Mitsubishi factory automation and factory robots, to further enhance their capabilities and efficiency:
Mitsubishi Factory Automation: Mitsubishi Electric offers a comprehensive range of factory automation solutions, including programmable logic controllers (PLCs), human-machine interfaces (HMIs), and servo motors. These technologies can be seamlessly integrated with automated conveyor systems to provide centralized control, monitoring, and optimization of manufacturing processes.
Factory Robots: Factory robots, such as robotic arms and automated guided vehicles (AGVs), can work in tandem with automated conveyor systems to automate material handling tasks, such as picking, packing, and palletizing. By leveraging the capabilities of factory robots, manufacturers can further increase efficiency, reduce labor costs, and improve overall productivity.
Applications of Automated Conveyor Systems
Automated conveyor systems find applications across a wide range of industries and sectors, including manufacturing, warehousing, distribution, and logistics. Some common applications include:
Assembly Lines: Automated conveyor systems are widely used in assembly lines to transport components and products between workstations, enabling continuous flow production and efficient assembly processes.
Distribution Centers: In distribution centers and warehouses, automated conveyor systems facilitate the sorting, routing, and distribution of goods, allowing for faster order fulfillment and improved inventory management.
Food Processing: In the food processing industry, automated conveyor systems are used to transport raw materials, ingredients, and finished products throughout the production process, ensuring hygienic handling and compliance with food safety regulations.
Automotive Manufacturing: Automated conveyor systems play a critical role in automotive manufacturing, where they are used to transport vehicle components, parts, and sub-assemblies along the production line, enabling efficient assembly and just-in-time delivery.
Conclusion
Automated conveyor systems are essential components of modern material handling automation, offering manufacturers and logistics providers a reliable, efficient, and flexible solution for transporting goods and materials throughout the production process. Integrated with advanced technologies like Mitsubishi factory automation and factory robots, automated conveyor systems help optimize operational efficiency, increase productivity, and drive business growth across a wide range of industries. As manufacturing and logistics operations continue to evolve, automated conveyor systems will remain a cornerstone technology for streamlining material handling processes and meeting the demands of today's dynamic market landscape.
Comments